Analyze – Optimize – Achieve
Unleash the full potential of your machinery: boost productivity and reduce operating costs
ViTA: the IIoT solution by Colosio
Discover more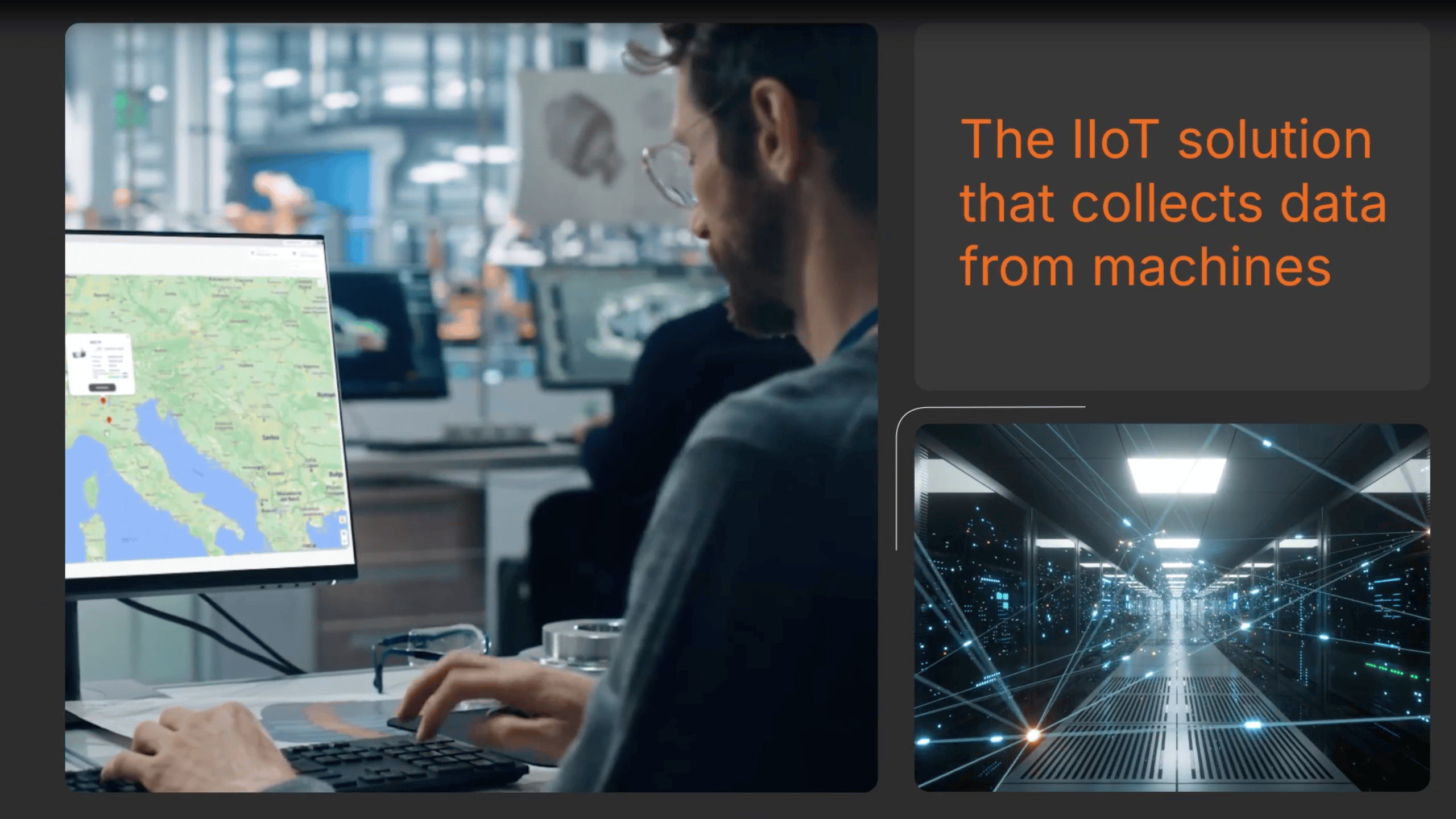
What is ViTA?
( INDUSTRIAL INTERNET OF THING )
The IIoT solution that collects data from machines
ViTA is the IIoT (Industrial Internet of Things) solution that transforms your data into valuable information and maximizes the quality of your production.
It combines Edge and Cloud technologies for real-time monitoring and analysis.
Main functionalities for different users
ViTA provides immediate access to KPIs, optimizing energy consumption with data-driven processes and integrating AI for sustainable and efficient operation management.
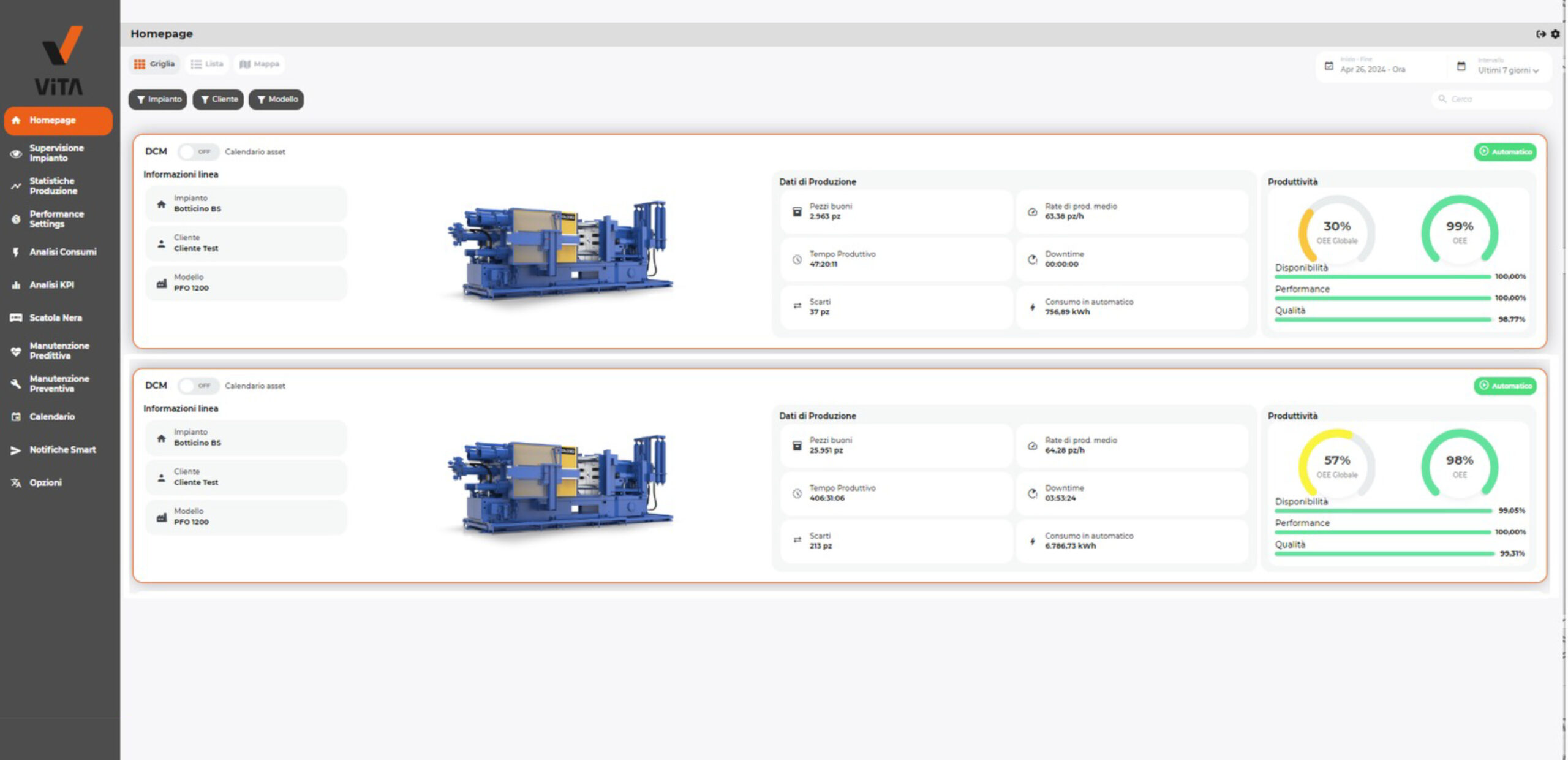
Production Manager and CEO
Monitor your plant status wherever you are and receive real-time KPI updates to improve productivity.
- Real-time monitoring of the status of all machines, even remotely.
- Real-time calculation of critical KPIs.
- Quick identification of plants in critical condition.
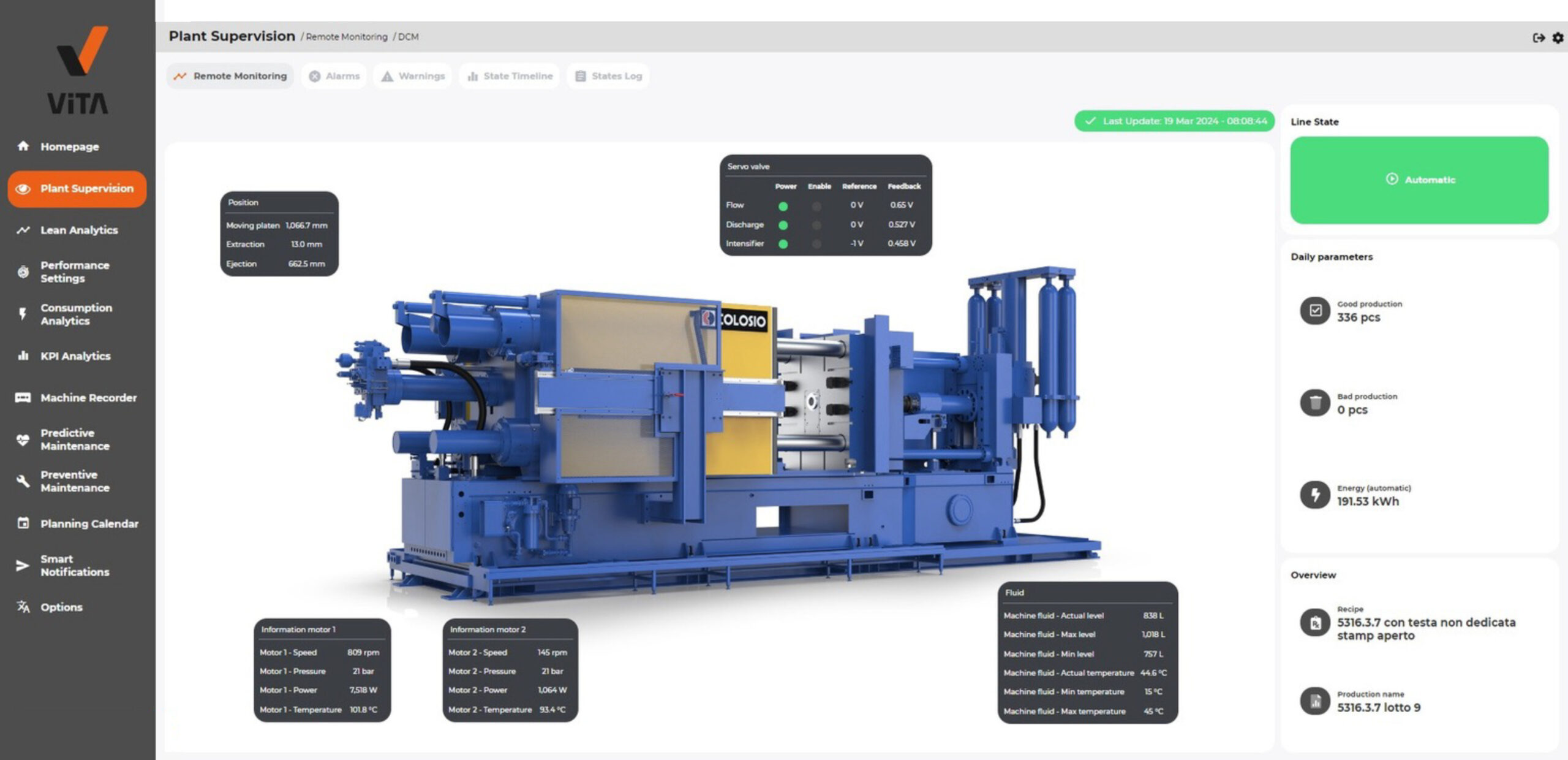
Head of Department and Field Engineer
Get access to precise details about every machine component and continuously monitor operating parameters for efficient management.
- Quick access to brief and extensive information in real-time.
- In-depth navigation of machine components (drill-down).
- Continuous monitoring of process parameters.
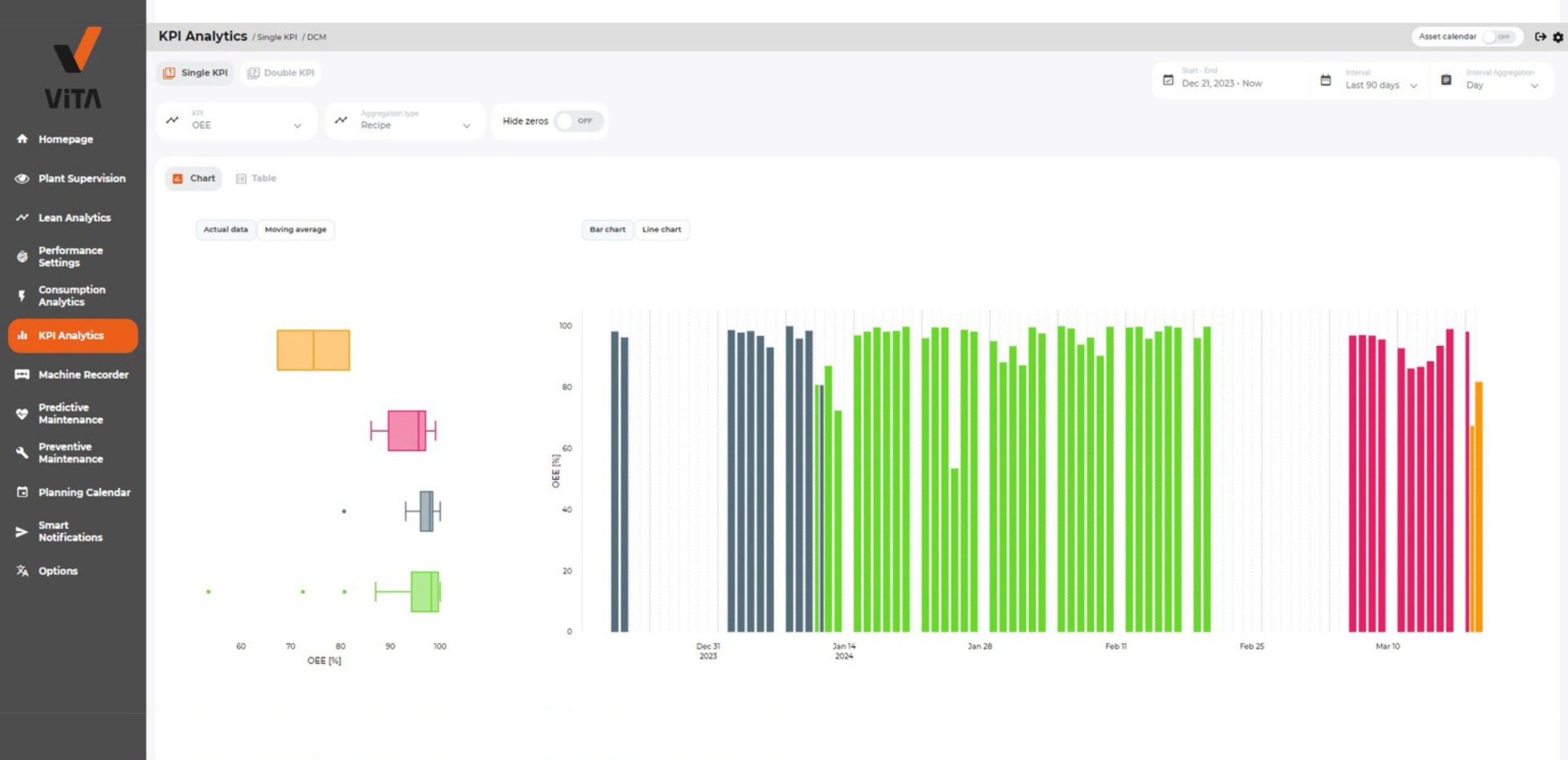
Lean Manager
Analyze energy consumption and optimize your plant’s performance by comparing data based on products and operational modes.
- Classification of actual plant consumption by product.
- Comparison of consumption based on different usage modes.
- Validation of optimization strategies based on real data.
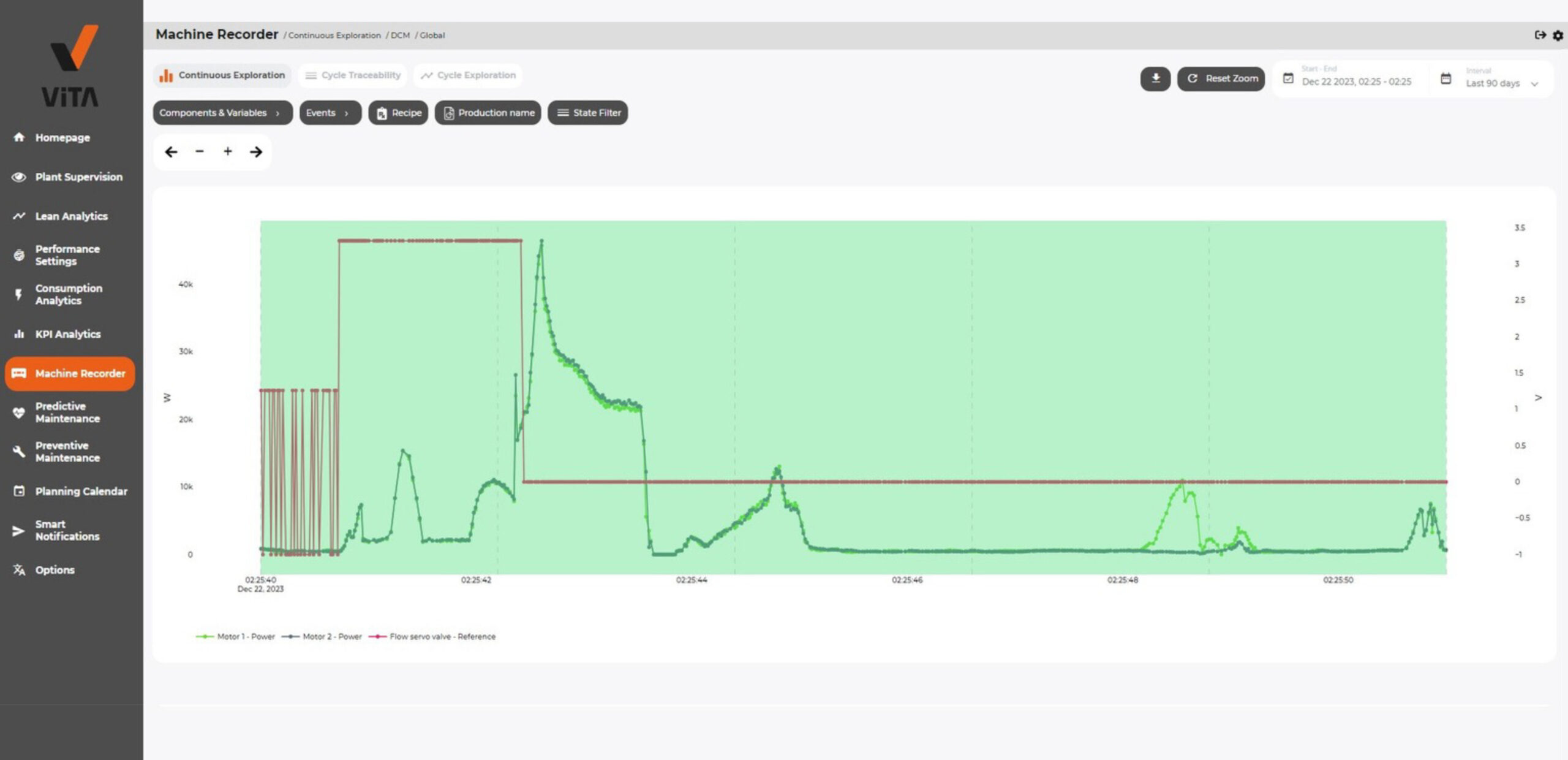
Maintenance Department
Schedule maintenance interventions based on real data and extend component lifespan, reducing costs and environmental impact.
- Maintenance status of components based on actual usage.
- Data-driven scheduling of maintenance activities to maximize component life (+20%).
- AI system for monitoring component status, with proactive detection of anomalies using a Grey Box approach.
Data Analysis
Constant monitoring and recording of data.
Analysis of recorded event history.
Analysis of inefficiencies using the Pareto approach.
Advanced KPI statistics and correlation between different metrics.
Predictive Maintenance
Continuous parameter monitoring:
Data is collected continuously and at high frequency, generating up to 500 GB of data per year. This allows detailed recording and analysis of process parameters.
Component lifespan optimization:
Extend component lifespan by at least 20%, reducing costs and environmental impact through maintenance planning based on data analysis.
Proactive and targeted interventions:
Through the use of AI and Anomaly Detection systems, it is possible to alert maintenance personnel proactively, intervening only when necessary to reduce downtime.
“Grey box” approach and use of AI:
The approach integrates physical and statistical models to monitor the components and identify critical conditions. Through a systematic troubleshooting process, malfunctions can be quickly detected, their causes identified, and effective solutions applied to optimize system operation.
Why the Cloud?
Security
Data is stored on Microsoft’s Azure servers, ensuring advanced protection.
Privacy
The data belongs to customers, safeguarding ownership and confidentiality.
Connectivity
Global and multi-device access for remote management wherever you are.